Wilson Tool Internationalは、CarbonのDigital Light Synthesis™技術を使用して開発されたQuickTap™タッピングツール用オイルリザーバーを導入しています。従来これらの部品は、高コストと長いリードタイムを要する冷延鋼板で作られていました。Wilson Tool Internationalは、Carbonを使用して最大60%のコスト削減、50%までのリードタイムの短縮、オペレータの安全性の向上を確認しています。
イントロダクション
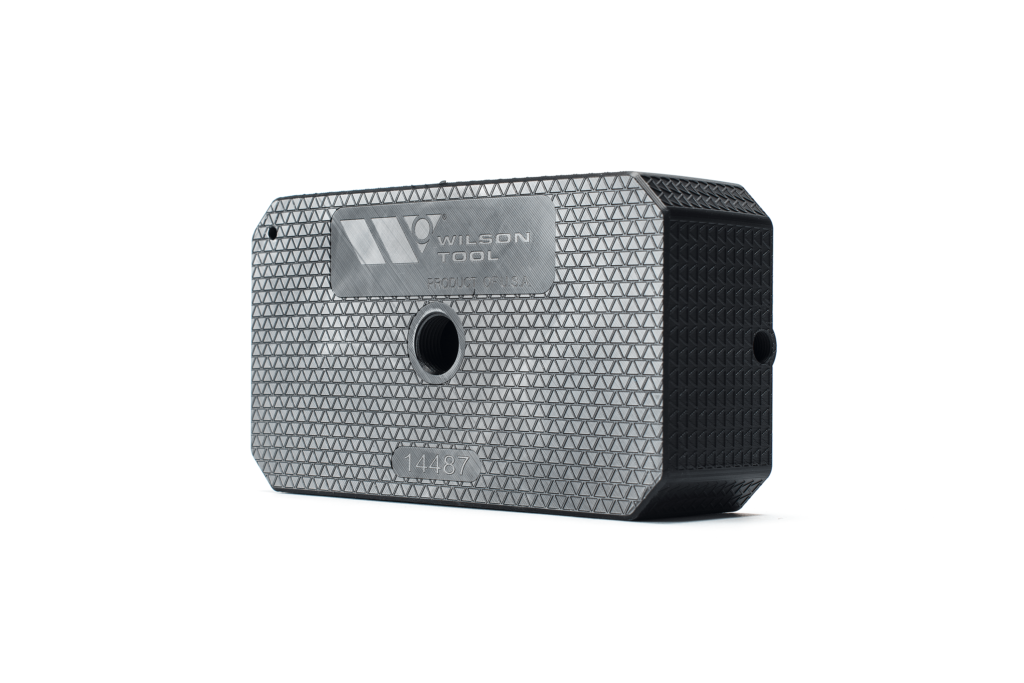
図1:CarbonのRPU 70で作られた新しいQuickTap™タッピングツールオイルリザーバー
Wilson Tool Internationalは、世界中のお客様に幅広いツールソリューションを提供しています。同社は、顧客が最も困難な製造上の問題を解決するのを支援するように設計され、カスタマイズされたツーリングソリューションと製品で知られています。Wilson Tool Internationalは、自社の製品にアディティブ製造(図1)を採用しており、CarbonのDigital Light Synthesis™技術の適用を含め、お客様のサービス機能として取り組んでいます。このケーススタディでは、Wilson Tool InternationalがCarbonと提携してより良く安価で安全な製品を構築する方法が記載されています。
需要に追随する
Wilson Tool Internationalは、これまで長いリードタイムと金属製オイルリザーバーの高コストによって、パンチプレス用のQuickTap™タッピングツールソリューションの需要に対応するのが困難でした。オイルリザーバーは、パンチプレスのタイプに応じて異なる形状の6タイプがあります。これは、Wilson Tool Internationalが顧客へ確実に納入するためには、高い在庫レベルを維持する必要があることを意味していました。しかし、在庫を高水準に保つことはコストと陳腐化のリスクを増加させたので、より良い解決策が必要でした。
タッピングツールは、板金製造プロセスにおける二次的な作業を排除することを目的としたWilson Tool Internationalのパンチプレス製品の中核部分です。これらの産業用工具は、他の金属部品を高速で生産するために不可欠です。ねじ穴の品質を維持しながら1分間で最大200ヶ所タップすることができるのです。タッピングツールは、タップ自体、モーター、オイルリザーバーで構成されています。タッピングツールの実際の動作をご覧ください。
6つのリザーバーは、冷延鋼板から打ち抜かれ、7~9の部品として成形された後、溶接して一体化されていました。継ぎ目が溶接されていたため、各タンクは加圧されたときに漏れないように厳密なテストプロセスを経る必要がありました。リザーバーが正しく取り付けられていないと、パンチプレスの可動部分に当たった際に工具および工具作業者に危険をもたらす可能性があります。
「私たちは、アディティブ製造が産業用工具の新しい道を提供する可能性があることを知っていました。オイルリザーバーの経験から、Carbonのプロセスと材料は基本的に新しいアプリケーションと機能を提供することが実証されました。」
Brian Lee
Wilson Tool International
R&D兼技術ソリューション部長
Wilson Tool Internationalがオイルリザーバーで直面した経済性と顧客サービスの課題への取り組みによって、より良い解決策を見出そうとするいくつかの試みが生まれました。その1つが、航空機グレードのアルミニウムから作られた完全に切削加工されたリザーバーです。6ヶ月間に複数の設計改良が繰り返され、製品の品質は基準に合っていましたが、コストとリードタイムの目標はWilson Tool Internationalが顧客に受け入れられる範囲を超えていました。さらに、各ユニットは依然としてテストされる必要があり、打ち抜き作業中の破損にともなう危険が依然として存在していました。ブロー成形も調査されましたが、部品が異なることにより金型コストが部品単価を上昇させ、製品の品質も許容できないため、これらのタイプのソリューションは実現にいたりませんでした。
コンセプトの探究と証明
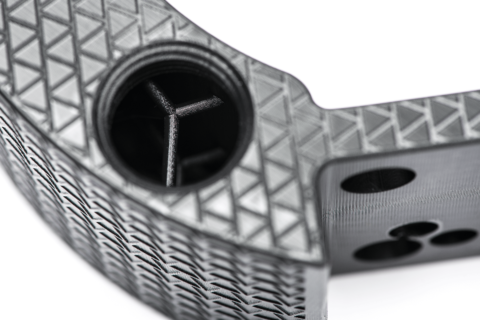
図2:カスタム表面仕上げと内部サポート格子を備えたタンクの詳細図
Wilson Tool Internationalは、アディティブ製造が適応できる部品とプロセスの改善について独自の調査を実施し、必要な品質、効率、スループットを実現できるプロセスを見出しました。同社はサンプル部品を見てCarbon技術に対する投資を決め、オイルリザーバーのプルーフオブコンセプト(POC)開発を優先しました。
このPOC部品は、オイルを保持し、既製の配管と接続し、十分な衝撃吸収を提供するという機能的要件を満たさなければなりませんでした。造形結果は再現性も必要でした。CarbonのRPU(硬質ポリウレタン)70材料による初めての造形で、Wilson Took Internationalは造形可能でかつ機能的、パーツコストが最大60%安価であることを認定しました。そして部品のリードタイムを最大50%削減することができ、金属部品が正しく取り付けられていないときにおこりうる破壊的な危険性はありませんでした。
彼らは設計を広く検証することにしました。CarbonのDigital Light Synthesis™技術の採用により、造形性向上のためにデザインを最適化し、内部ラティスで機械的剛性を付与し、さらに特徴的な表面仕上げを導入することによって、3ヶ月で5回の設計改良を行ったのです。彼らはまた、部品番号とブランド名を部品ファイルに追加しました。最大のタンクでは、追加の機械的剛性を提供するために内部ラティス構造を付与しました(図2)。並行して、Wilson Tool Internationalは熱的および化学的安定性の両方について部品を検証しました。彼らは低温(0°F)と洗浄のためのナフサへの暴露の両方に懸念を持っていました。
そして生産へ
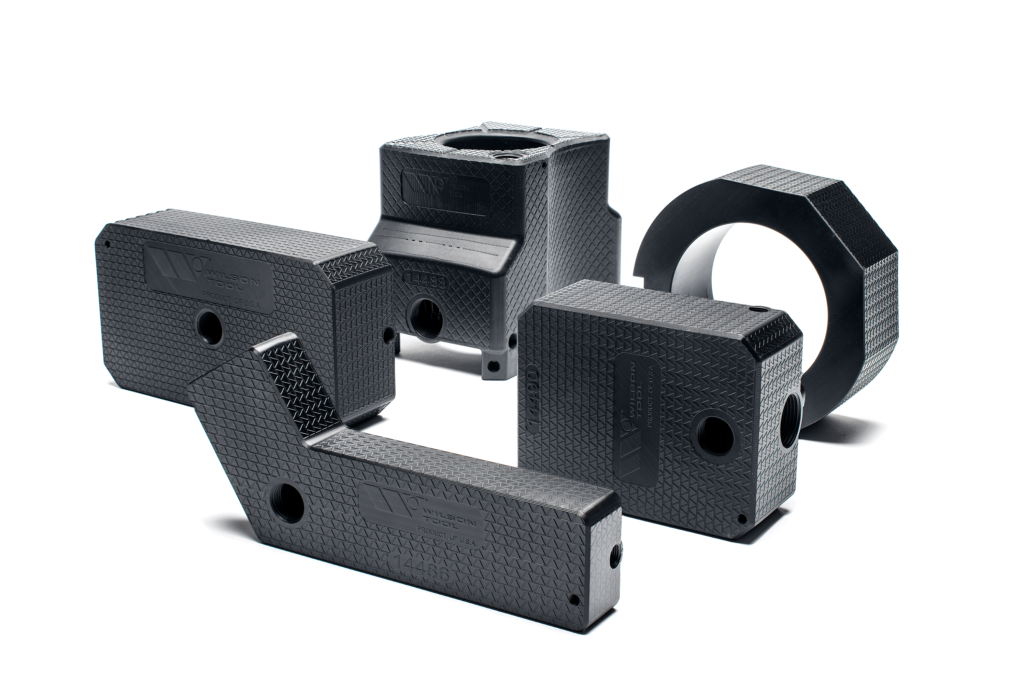
図3:Wilson Tool Internationalは、Carbon技術に基づくQuickTap™タッピングツールタンクを発売しました
RPU 70がすべてのテストに合格したとき、彼らはオイルリザーバー部品を生産用に認定し、リザーバー全体に新しい材料を広く実装しました(図3)。低価格と短納期、よりよく安全なこの部品のメリットは、消費者にも拡大しています。