「あなたがまだ可能ではないことを信じようとしているなら、可能であることを再考してみる必要があります。それはそこに到達できる唯一の方法です。Carbonとのパートナーシップは、Vitamixにとって非常にエキサイティングです。これは、毎日可能かもしれないことを再考するのに役立っています。」
Jodi Berg
Vitamix 社長兼CEO
Vitamixは家庭用および商業用の高性能ブレンディング機器の世界的リーダーです。100年近い製品設計と開発の歴史を持つVitamixは、その性能、汎用性、使いやすさで知られる革新的なブレンダー製品によって、健康的なライフスタイルへの動きの拠点となっています。最近、Vitamixは、The Technology House(TTH)とCarbonと提携し、商業的な環境で使用される特殊ノズルを再設計しました。この特定のノズルは元々、面倒な組み立てを必要とする複数の部品を使用して、射出成形プロセスのために設計されていました。
このケーススタディを読むと、VitamixがTTHおよびCarbonと協力して、以前のノズルより10倍の耐久性と30%の経済性を備えた革新的なノズルをどのようにしたら完全に再設計して生産までできるようになったのかが学べます。Vitamixは、数万個のノズルを店舗ネットワークに展開しています。
既存のノズルの課題
Vitamixは、店舗環境で市販のブレンダーのすすぎに使用される特殊ノズル(図1)を製造しています。これらのマイクロ流体ノズルは、300ミクロンの孔から加圧水を噴射するように設計されており、漂白剤、洗剤、および他の消毒剤を定期的に噴出し、ブレンダー容器のすばやく効率的なすすぎを行います。したがって、これらのノズルの機能要件は2つあります。
- 非常に特殊で細かい形状が要求されるパターンから、高速で圧力をかけたジェット水を噴射する強固ななマイクロ流体設計
- 信頼性、具体的には、商業的な食品サービス環境において毎日の摩擦、磨耗操作に耐える能力
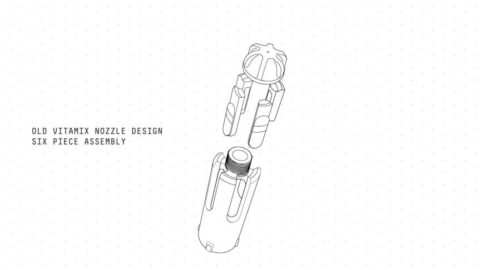
図1:古いノズル設計は、6つの個別の射出成形部品から組み立てることを意図していました
レガシーノズルは、製造レベルで射出成形プロセスを用いる6つの部品が設計された、光造形(SLA)、選択的レーザ焼結(SLS)、溶融堆積モデリング(FDM)、および真空注型を含むさまざまな試作が行われました。射出成形は、一般に、高い金型費、部品のリードタイムの遅延、部品の設計や反復の自由度が大幅に低い、などの課題があります。
Vitamixのミッションステートメントは、「世界最高の性能と信頼性の高いブレンドソリューションを設計、開発、生産することにより、生活への寄与を築きます。」というものです。Vitamix製品開発チームは、アディティブ製造のリーダーであるTTHとCarbonとともに、革新的なマイクロ流体ノズルを開発するために部品設計と生産を完全に再構築します。
新製品の開発姿勢
限られたノズル開発時間とフィールドテストに挑戦するため、Vitamixは、オハイオ州に本拠を置く製造受託会社であるTTHに連絡をとりました。TTHは複雑なマイクロ流体ノズルを見て、CarbonのSpeedCell™システム(MシリーズプリンタとSmart Part Washerを含む)と硬質ポリウレタン(RPU)材料を使用して、6つの個別部品を3D造形することに決めました。当初の問題解決手法は、金型コストを削減または低減し、部品のリードタイムを短縮し、形状忠実性を有する部品を供給しようとするもので、サプライヤまたは金型によらず堅牢な機械的特性をも示すことでした。この機能の組み合わせを提供できる他のプロセスなどありません。
アプローチの仕方は、フィールドテストを行った後、ノズル設計を繰り返しました。射出成形のサプライヤを使用して数か月要するのに対し、3D造形では数時間で現場対応部品を造形できます。しかしながら、このアプローチでは、依然(射出成形のために設計された)複数部品の組立および高い製造負荷が必要でした。
Vitamixのエンジニアは、顧客の期待に応えるために時間的プレッシャーを受けていました。VitamixとTTHチームは、解決に集中したところ、CarbonのDigital Light Synthesis™技術のすべての機能を十分に活用していないことに気づきました(図2)。VitamixとTTHのエンジニアは、6部品からなるノズルを、組立が不要な一体化部品として全体を製造する、という野心的な目標を設定しました。Carbonの材料は、漂白剤への優れた耐性を提供しながら、要求された機械的特性を満たしました。Carbonの技術は、高圧流体というノズルの性能要求のために重要な要素である、優れた表面仕上げを有する複雑な形状およびチャネルを製造することができるのです。
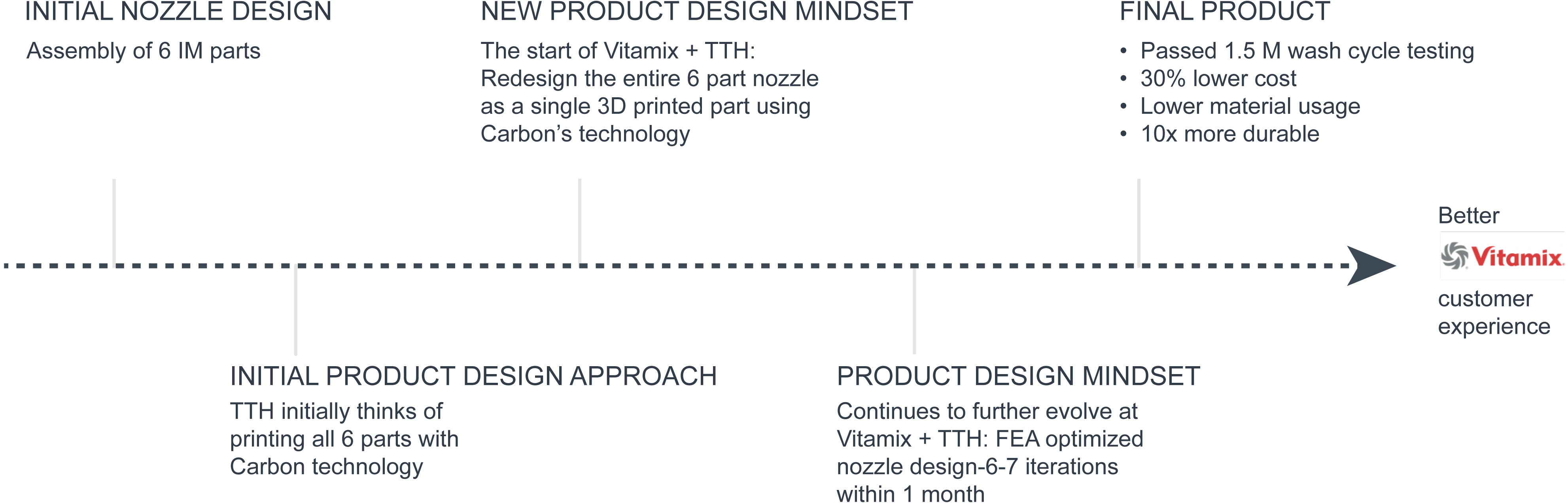
図2:Vitamix + TTH + Carbonの製品設計の考え方の進化により、優れた顧客体験を実現する優れた製品を提供
新しい製品開発にはつきものですが、Vitamix、TTH、Carbonのエンジニアは、新しいノズル設計の機能的な性能と信頼性、ノズルの製造可能性に関する多くの課題に直面しました。TTHとCarbonのエキスパートが協力して、造形プロセス開発における問題を解決しました。エンジニアは、ノズルと複雑なマイクロ流体チャネル構造に300ミクロンの穴を空けて、CarbonのソフトウェアとMシリーズプリンタを使用して設計自由度と設計最適化の壁を乗り越え、6つの個別部品のアセンブリではなく、これらのノズルを一体化した部品として3D造形しました。
その結果、30%少ない材料で完全に最適化されたノズルが得られます。Vitamixエンジニアリングチームは、実使用環境での消耗への耐久性を保証するために、設計開発の各段階で広範なラボおよびフィールドテストを実施しました。Carbonエンジニアは、Mシリーズプリンタでの量産規模の造形性を確保するために、ノズル設計する上での有限要素解析(FEA)を活用しました(Figure 3)。
この製品開発で注目すべきもう1つの側面は、革新のスピードです。製品エンジニアは、迅速な設計と最終的な造形性の検証を可能とするCarbonのデジタル製造機能を活用して、わずか4週間で6~7回のノズルの設計改良に成功したのです。
射出成型アプローチの場合、1回の設計変更に伴う金型修正には8~10週間(金型に問題が無い場合)を要してしまうこともありました。Carbonの設計改良と造形性によるスピードは、従来の製造アプローチと比較して、エンドツーエンドのデジタル製造の実力を際立たせています。TTHとCarbonによる、製品開発への”Fail fast”アプローチの適用はVitamixが堅固な生産ソリューションをはるかに迅速に実現することに繋がりました。
成果
Vitamixの最適化されたノズル(Figure 4)は、複数部品の組み立てが不要な単一の3D造形部品です。射出成形などの従来の製造方法ではこれを達成できません。革新的なノズル設計は材料を少なくし、軽量で、金型を必要とせず、手作業を55%削減して製造します。その結果、Vitamixは従来設計と比較してノズルの最終コストを約33%削減することができます。さらに、Vitamixは、内部およびフィールドテストプロセスの早い段階で3D製造アプローチの可能性に気づき、射出成型で必要な金型のコスト、エンジニアリングリソースや時間の浪費を回避することができました。
広範な品質試験の結果、Vitamixエンジニアリングチームは、複数部品による旧モデルと比較して新しいノズルが10倍以上の耐久性を有するものと結論づけました。事実、Vitamixの厳しい品質管理プロセスの一環として、新しいノズルは150万回以上のサイクルテストにひとつの欠陥もなく合格しました。Vitamixは、テスト結果に満足し、Carbonの技術と材料を使用した新しいノズル設計が、より丈夫で効率的な洗浄ノズルという、求めていた生産ソリューションであると確信しました。ノズルはオハイオ州クリーブランド近郊のTTH施設で製造されており、Vitamixは米国内で数万個を展開しました。
様々な産業分野で製品開発されているチームであれば、同様の製品設計の考え方をその製品に活用し、より優れた性能と経済性をもたらすデジタル最適設計を行うことができます。