Carbonは、エンドユーザーの知見を参考とし、顧客の最終製品製造を可能とするアディティブマニュファクチャリングによるソリューションを開発しています。 材料科学、ソフトウェア、ハードウェアにおける革新とエンドユーザーのニーズとを融合させるというCarbonの理念は、adidasのミッドソールに採用された類の無いエラストマー材料のラティス構造として結実しました。ここではadidasのミッドソールの事例を参考に、顧客ニーズに応えたラティス作成機能の詳細をご紹介致します。
ラティスのイノベーション
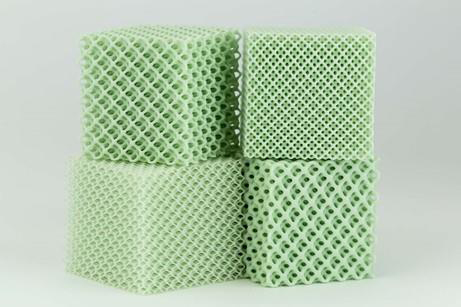
図1:Carbonのラティス作成例
Digital Light Synthesis™(DLS™)はデジタル光投影技術、酸素透過光学技術、弊社独自設計によるプログラマブル樹脂技術を活用して開発された、先駆的且つ画期的なアディティブマニュファクチャリング技術です。 これにより、高機能で耐久性に優れた最終樹脂部品や製品の開発プロセスを変革します。さらには造形速度は既存のアディティブマニュファクチャリング技術を大きく凌駕しています(最大100倍)。
Carbonの技術では、優れた表面仕上げと異方性の無い機械的特性を有する、高解像な部品を作成することが可能となります。 ソフトウェア技術によりMシリーズプリンタと多様なプログラマブル樹脂は独自のラティス(図1)を生成し、ヘッドセットの発泡材、靴のミッドソールやシート材の代替を可能とします。 顧客ニーズに最適なラティスを自在に設計し生成する機能はCarbon独自のものです。Carbonは初めて、単一の製品内に複数の機能的領域を形成し、適用用途の要求に応じて個別に機械的特性を付与することを可能としました。
adidasの事例
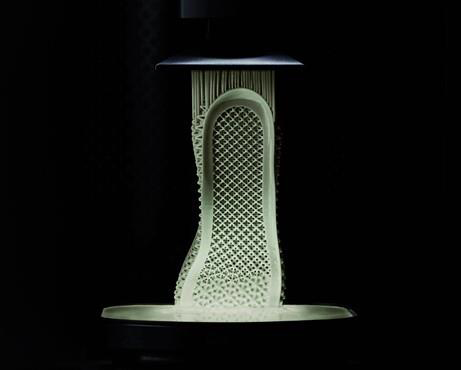
図2:CarbonのMシリーズプリンターで造形される、変化するラティス構造を有するadidasのFuturecraft 4D ミッドソール
Carbonの革新的なラティス生成技術に強く魅了されたadidasは、本格的ランナーの要求に応える性能と快適性を有するミッドソールを開発するため、Carbonとの共同開発に踏み切りました。adidasはシューズ全体のクッション特性を最適化し、特注のアスレティックシューズの提供が可能な技術プラットフォームを探していました。ミッドソール設計の豊富な経験とデータを有するadidasは、従来型の製造方法の制約を受けない新たなものを創造したいと考えていたのです。
従来の技術では、この様な複雑で高機能なデザインや、通常複数パーツの組み合わせによってのみ可能な多様な機能領域を、単一のミッドソールに組み込むことは不可能でした。そもそもこの方法は複雑となりコストもかかるうえ、品質面の懸念もありました。CarbonのDigital Light Synthesis™技術はこういった課題を解決し、新時代のシューズ製法をadidasにもたらしました。その成果がFuturecraft 4D (図2)です。 同時に、デジタル化されたシューズ部品の生成プロセスは従来の試作や金型を不要としました。 Carbonの技術により、adidasは単一のミッドソールで動き、クッション性、安定性、快適性といったニーズに細かく対応することが出来る様になったのです。さらには開発の過程でのデザイン改良は50回以上と、これまでの開発期間では不可能なほど大幅な改良頻度向上を実現しています。加えて両社の技術者はほぼ150もの樹脂レシピをテストしています。
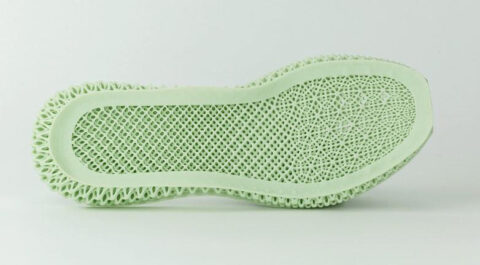
図3:単一のミッドソール内に、異なるラティス構造により複数の機能領域を形成
採用された材料はUV硬化樹脂とポリウレタンのブレンドです。硬度のあるエラストマーによりラティス構造を生成し、優れた耐久性と外観を有する高性能なミッドソールを作り上げることが可能となりました。従来手法では実現不可能なほどの高頻度なデザインや材料の改良は、エンドユーザーの知見を考慮した3Dプリンティングソリューションを提案するというCarbonの理念の証でもあります。またFuturecraft 4Dのリリースはシューズにかつてないレベルの性能を付与することとなりました。ミッドソール部分は機能別に精密に設計された領域を有しています(図3)。ヒール部分と前足部とでは異なるラティス構造を有し、走行中に必要な異なるニーズに応えています。Carbonの技術が単一の高機能部品により、adidasのニーズに対応することを可能としました。adidasによる生産拡大に際しては、Carbonはアスリートにより良い使用体験を提供するための重要な役割を担うことになります。将来的には、両社はアスリート毎の個別のニーズと生理学的データに合わせた、カスタムメイドの機能的製品を提供することが可能となるでしょう。
ラティスのメリット
Futurecraft 4D における成功は、adidasのデザイナーだけでなく他の産業の商品開発やものづくりの可能性を広げる好例です。ヘルメットや矯正用クッション、車載シート、バイクシート、ヘッドセット等の設計者は初めて、発泡素材を効果的に代替しまたは補完し得る微調整が可能なラティスを利用することが出来る様になりました。Carbonの革新的ラティスにより設計者は、従来の製造技術では不可能であった最も複雑なラティス形状でも物理的に実現 することが出来る様になるのです。 Carbonの技術により可能となるラティス構造のメリットを下記に要約します。
設計の簡素化
Carbonは同一部品内で様々なラティス構造を作成することを可能とし、他に類を見ないデザインを産み出します。これまでは、エンジニアは複数のコンポーネントを組み合わせ、同一の最終部品の中に異なる特性を付与しなければなりませんでした。この複雑さは設計変更、金型作成および組み立てのリソースを必要とする上、しばしば品質問題を引き起こします。adidasのミッドソールの例で特筆されているように、Carbonを使用すると、単一部品中で様々な機械的特性と美観を兼ね備えたラティス構造を迅速に設計することが可能です。このユニークな機能により、新製品設計の可能性が広がり、最終的には差別化された最終製品の作成が可能となるのです。
通気性の付与
Carbonラティスの革新とそれによって得られるオープンセル(図1)により、顧客は熱特性が改良された最終製品を製造することが出来ます。シート、肘掛け、ヘッドセット、腰掛パッド、整形外科用サポート等の用途では、通気性の付与により快適な温度を維持することが出来ます。こういった用途での熱制御は、理想的な使用体験にとって不可欠であり、オープンセル構造による放熱がそれを可能とします。
洗浄性
発泡材の様な素材の洗浄は手間がかかります。さらに発泡材は水分が残り、乾燥に時間がかかることは望ましくありません。その一方で、Carbonのラティス構造は洗浄も容易で水分も残らず、洗浄後も速やかに使用することが可能です。
まとめ
adidasとの関係は、Carbon独自のラティス造形機能と、ラティスを設計し造形するというadidasの要望とを組み合わせたことの結果です。 現在では正確に設計された機能領域をミッドソールに適用させることにより、動き、クッション性、安定性、快適性といった特定のニーズに応えることが出来ます。ケーススタディでご紹介したバイクシート、整形外科用パッド、ヘッドセットなどの他の用途は、製品開発担当がCarbonの技術を新部品や新製品への適用しようと考えた時に、単なる出発点となるのでしょう。広範な樹脂ラインナップを使用してラティス構造の精密設計と造形を実現することが出来るCarbonは、ラティス構造の適用によりエンドユーザーエクスペリエンスを向上させ得る用途探索という困難な課題に取り組みながら、既存材料と同等の特性を達成しなければならない製品開発チームの力になることが出来るでしょう。