製品の差別化が絶えず要求される現在、企業にとって製品を継続して差別化する必要があるとき、パーソナライズ商品に対する需要とマスカスタマイゼーションの必要性は持続的なトレンドとなっています。 企業は、カスタマイズ商品の費用対効果の高いソリューションとしてデジタルマニュファクチュアリングに注目しています。それは、独自の価値を示すと同時にプレミアム価格を実現できるソリューションです。MyFit Solutionsがカスタマイズされたイヤホンチップを高い費用対効果を維持しながら生産するために、認定Carbon Production Network PartnerであるErpro GroupのCarbonデジタルマニュファクチュアリングプラットフォームをどのように活用しているかご覧ください。
ワンサイズでは全ての人にはフィットしない
イヤホンは、スピーカーが外耳道の内側にぴったりはまり、音波がより直接鼓膜に当たるようフィットさせます。標準仕様イヤホンに最適なサイズの耳を持つ人もいますが、多くの人にとってフィット感が悪く、その結果、イヤホンが脱落したり不快に感じたりします。 カスタマイズイヤホンは、現状、聴覚訓練士からのみ入手でき、一組150ドルから250ドルと非常に高価なままです。これはカスタマイズ商品の製造に、コストの高い従来の製造方法を使用しているためです。
MyFit Solutionsは、ヘッドホンとは異なり、耳に万能なサイズがないことを知っています。 そのため、顧客が耳をスキャンできる高度な拡張現実スマートフォンアプリを開発し、3Dモデル生成に必要な耳の内側の形状を読み込めるようにしました。 次に必要となったのは、カスタムフィット製品をコスト効率よく生産できる実行可能な製造ソリューションでした。
オンデマンド在庫
MyFit Solutionsは当初、製造ソリューションとしてシリコンモールドを検討しました。しかし、この方法では望ましい結果を得られず、カスタマイズ用途には高価すぎました。 そこで、MyFit Solutionsはデジタルマニュファクチュアリングソリューションを検討した結果、Erpro GroupのCarbon のDigital Light Synthesis™(DLS™)技術を備えたErpro Groupの生産技術が、しっかりした装着感、優れたオーディオ性能、最適な心地よさを提供するテーラーメイドイヤホンチップの製造に理想的であることを見出したのです(図1 )。
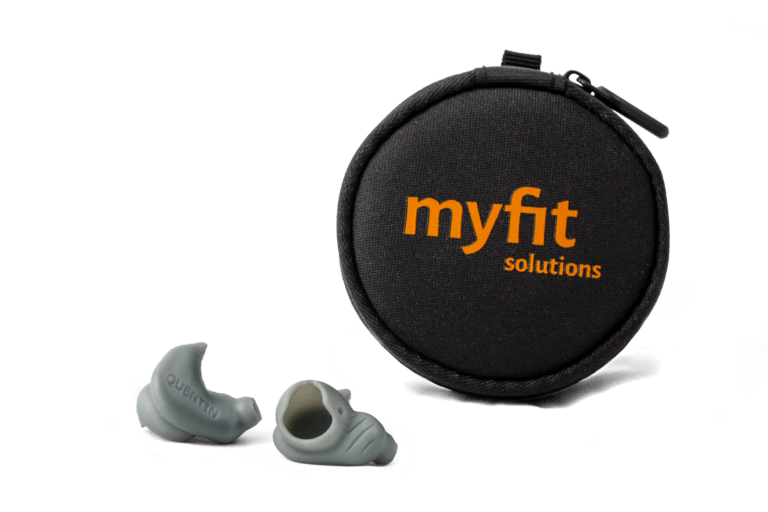
図1:Erpro GroupにてCarbonデジタルマニュファクチュアリングプラットフォームとSIL 30で製造されたMyFit Solutions カスタマイズイヤホンチップ
生体適合性材料
Erpro Groupは、Carbon SIL 30 material(シリコンウレタン)がMyFit Solutionsのイヤホンチップに適していると考えました。生体適合性があり、触り心地のよい製品をカスタマイズ用途で造形できるからです(図2)。 さらに、その引裂き抵抗とソフトタッチにより、この素材がイヤホンチップに最適な耐久性と心地よさをもたらすことが判明したのです。
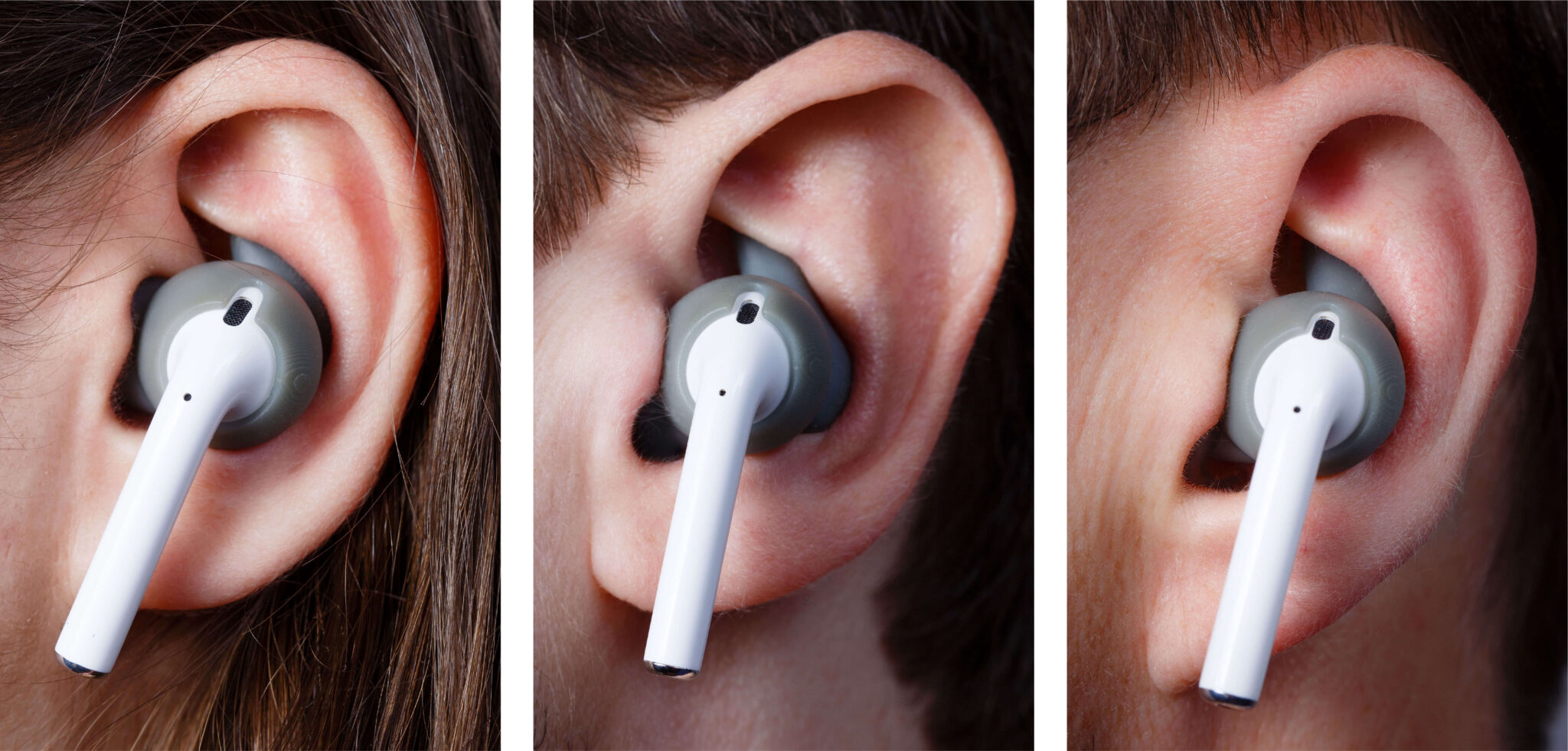
図2:生体適合性がありソフトタッチの Carbon SIL 30 製 MyFit Solutions カスタマイズイヤホン
マスカスタマイゼーション
MyFit Solutionsは、Carbon DLS™技術を活用して複数の標準イヤホンブランドに適合するイヤホンチップを製作し、さらには追加費用なしでパーソナルデザインを追加することもできます(図3)。Apple AirPods、Apple EarPods、Bose StayHear Tipsを始め、多くのイヤホンブランドとの互換性があり、提供されるパーソナルデザインには、機能的で審美的なテクスチャ、そして、チップごとに固有の文字(名前やイニシャルなど)を刻印するオプションが含まれます。
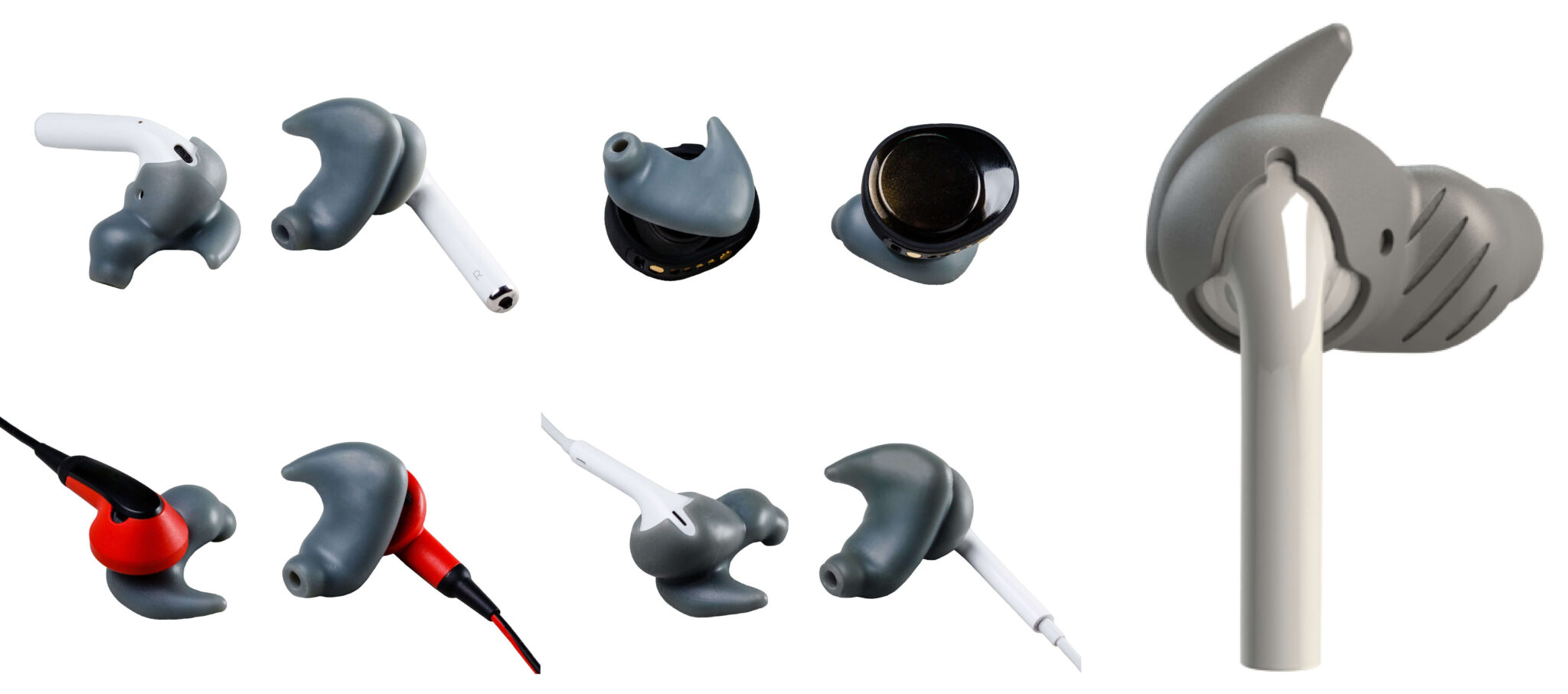
図 3: 適合可能なイヤホンブランド(左)パーソナルテクスチャ付与(右)
費用対効果の高いカスタマイズ+市場投入までの時間の短縮
Erpro Groupは、Carbonデジタルマニュファクチュアリングプラットフォームを活用して、MyFit Solutions用カスタマイズイヤホンチップを3日以内に費用対効果の高い方法で製造することが可能となりました。また、これらのカスタマイズされたチップは、以前のカスタマイズイヤホンソリューションの半分以下の価格で市場に提供することが可能です。 さらに、Erpro Groupの生産技術は、MyFit Solutionsの製造現地化を実現し、出荷コストを究極まで削減し製品と消費者の距離を縮めています。
MyFit Solutionsは現在、2〜3週間ごとに50組を製造していますが、需要が増加し続けているため、さらなる増産を見据えており、近い将来には生産が倍増するものと予測しています。
カスタマイズされたイヤホンチップを入手したい方はMyFit Solutions websiteで注文できます。