実際のラインや治具をご紹介いただき、一つ一つの工程やそこでの治具の使い方、製作の工夫などを丁寧にご説明いただいたので、これから治具を3Dプリンターで内製化しようとご検討の方は、ぜひご一読いただきたい。
(聞き手:シェアラボ編集部、語り手:EIZO株式会社 製造部 生産技術課 専 雅晴氏、提供:JSR株式会社)
EIZOが作るハイエンドなモニター製品群
―EIZOさんはデザイナーが使うハイエンドなモニターを製造されている印象があります。
そうですね、EIZOでは一般的なモニターだけでなく、色の再現性が高いカラーマネージメントモニター、産業分野向けや医療機関向けモニターなども製造しています。
![]() カラーマネージメントモニター |
![]() 医用画像表示モニター |
![]() 本社工場(石川県) |
![]() |
本日お越しいただいた本社工場では主に少量多品種生産に取り組んでいまして、私たちの生産技術部門では、新しい生産方式の検討から設備の導入や改善を担当しています。
導入のきっかけは製造ラインの新設
―少量多品種生産となると、生産技術の方への生産準備の負荷も高そうですね。Carbon社の3Dプリンターを導入した目的は治具製作だとうかがっていますが、直接のきっかけは何ですか?
![]() |
![]() |
以前は治具を自分たちで設計して、加工は外注することが多かったのですが、Carbon社のM2より以前に導入したFDM方式の3Dプリンターで治具製作をおこない一定の手ごたえを感じていました。そんな中で新規製造ラインの立ち上げがありまして、このタイミングで3Dプリンターの利用範囲を拡大しようと考え、Carbon社のM2プリンターを導入しました。
製品設計部門が先陣を切ってというわけではなく、生産の際に使う治具などに焦点を当て、導入効果を想定して導入している点が他のCarbon社の事例と違うところかもしれませんね。
2年で200種類以上の治具を製作
―導入して2年でどのくらいの治具を製作されましたか?
そうですね、ざっと200種類以上製作しました。少量多品種生産に取り組んでいますので、新しい製品が起こると、生産用の治具も必要になります。いままでのFDM方式の3Dプリンターは造形に失敗することもあれば、製作にも時間がかかったので、一部にしか活用できていませんでしたがCarbon社のM2プリンターは造形が安定していて、以前に使っていたFDMよりかなり高速です。活用の範囲は広がっています。
―どんな治具をつくってきたか、いくつかご紹介いただけますか?
ここに並んでいる治具がそうなんですが、コストパフォーマンスが大きく改善できたのが、こちらの固定治具です。
![]() |
![]() |
この固定治具は1セット分など、必要なだけしか製造しないこともあって、今まではアルミのブロックを両面削り出して業者さんに加工してもらっていました。そのため費用もそれなりに高く、一つ数万円程度の費用が掛かっていました。これがCarbon社の3Dプリンターで造形すると一つ千円もしません。かなりのコストダウンを実現できています。
―非常に大きなコストダウンですね!
コストも大きく削減できましたが、調達にかかる時間も大きく短縮できています。納品されるまで2週間から3週間はかかっていた固定治具が数日以内に内製できます。失敗したらまたやり直せるという点で安心感もあります。
―内製ならではのメリットですね。造形は専門の造形者の方が行いますか?それとも設計される方がそのまま造形も担当していますか?
![]() |
![]() |
![]() |
設計者が直接造形も行います。いま10人以上が使っていますが、自分が設計し、自分で造形します。プリンターから取り出し、洗浄後に熱処理を行うところまで自分の作業で行います。治具製作のためにしか使っていませんが、いま週4日はなんらかの形で稼働している状況です。
―かなりの稼働率ですね。それに設計者が自分で造形まで行うと、3Dプリンターを使った造形の実際のところも把握できて設計しやすくなりますよね。
自分で設計から3Dプリンターでの造形までやってみて、治具製作が非常に楽になりました。というのも、設計上の制約がほとんどないんです。金型で作ってもらう際に気を付けなければいけないことは、3Dプリンターで作れば、全く意識しなくてもモノが作れます。このロボットハンドは、カメラなどのセンサー類をロボットアームに固定するために用意しているのですが、設計的には非常にシンプルです。
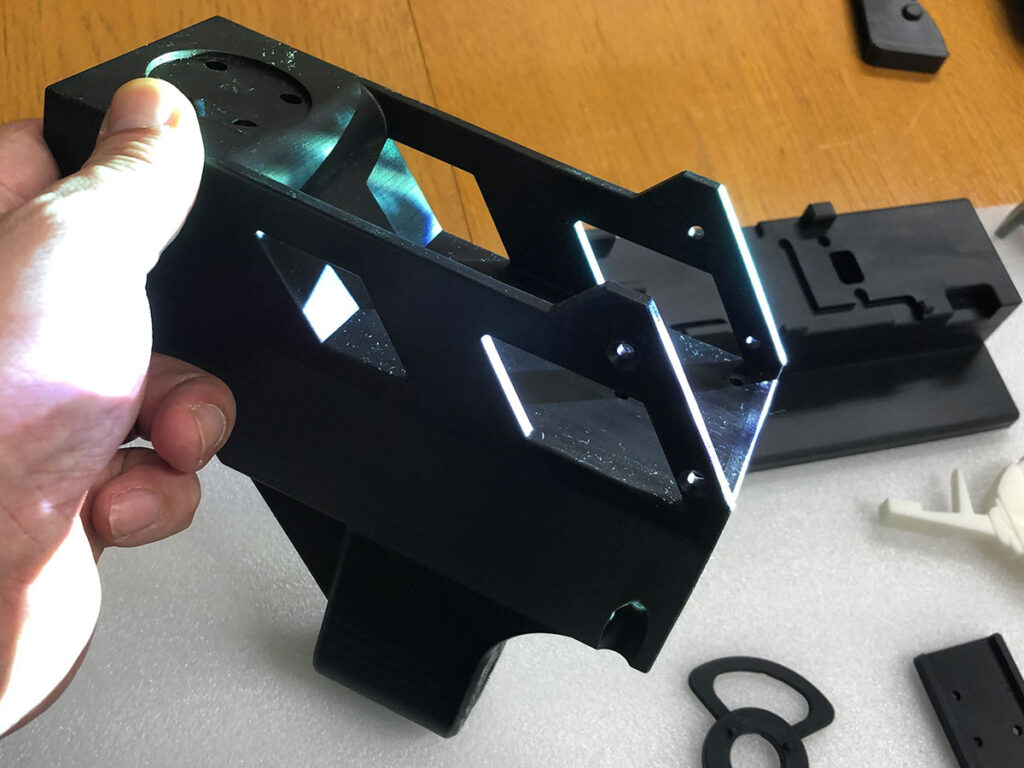
検査用ロボットのハンド部
固定するセンサーやカメラのサイズと固定金具を止めるビス穴をあけて、アームに固定する穴をあけてという形で、やりたいことをそのまま形にしているだけなんです。設計にかかる期間も他の工法にくらべて非常に短く済んでいます。
―工法に縛られていた設計の制約がなくなったということですか?
そうですね。本当にこの部品は作れるのか、と考える必要はないですね。どんな形状でもモノがつくれてしまうので。逆に私たちは「3Dプリンターならではの設計」にはあまり取り組んでいません。社内で使う治具なのでそこまで凝る必要がないといいますか、必要な機能と形状を備えた治具が、現状でも早く安く用意できるので、目的としては達成できているんですよね。
―なるほど。そんな中で何度も試行錯誤した治具はありますか?

造形したハンドは検査用ロボットに取り付け。検査の自動化で活躍
先ほどご紹介したロボットハンドは試行錯誤を繰り返しました。ロボットハンドは市販の部品もあるのですが、大半の場合、改良が必要になります。今回は完成したモニターの検査の一部を自動化するためにカメラやセンサーをハンドに取り付けています。
検討を進める中で、カメラやセンサーの種類や距離を変更しながら進めて行くので、ロボットハンド部は変更を繰り返して、実際に製作して、動作を見ながら完成度を上げるというサイクルを繰り返します。Carbon社の3Dプリンターは設計制約が少なく造形時間も短いので通常よりも手間も少なく、短い時間で完成させることが出来ました。
―ここまでお話をうかがってきて、3Dプリンターが、かなり業務になじんでいるご様子が伝わってきました。
3Dプリンターを使うことは、私たちにとって当たり前になっています。逆に他の方法で調達できる物でも、手軽に作ることができるので、四角いブロック形状のようなものまで3Dプリンターで作ってしまいます。
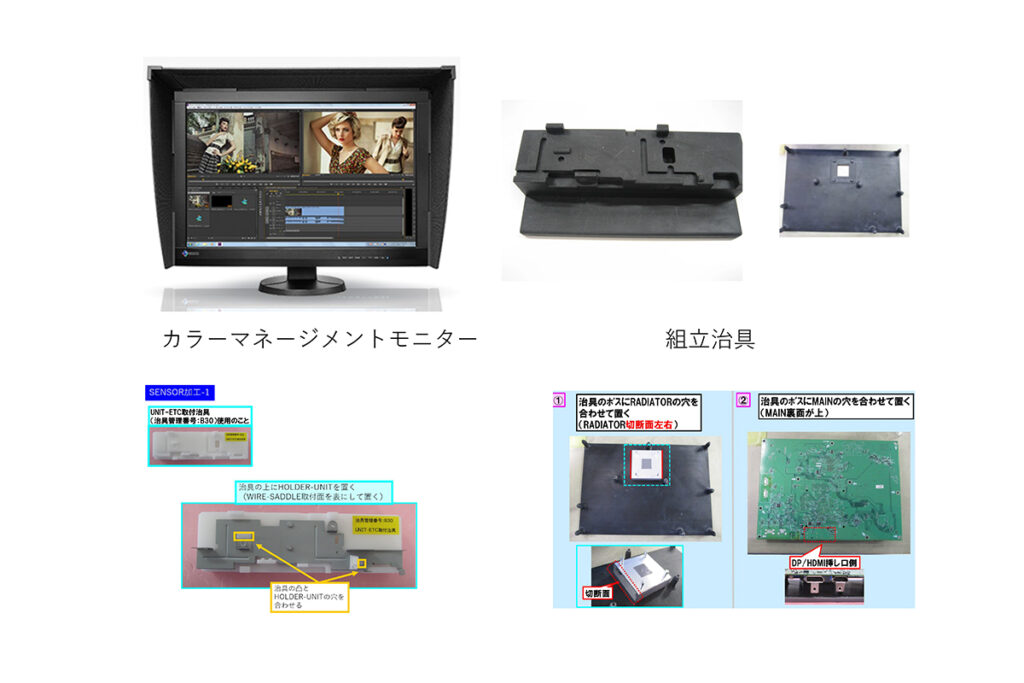
高付加価値製品であるカラーマネージメントモニターの組み立てで活躍する治具
―3Dプリンターで製作する治具は1種類あたり、だいたい何個ぐらい用意するものですか?
少量多品種ラインのために新規製作する治具は、1セットから多くても数十個セットというのが多いです。ですが最も多く作ったのは300個ですね。
![]() |
![]() |
これはRFIDタグを製品の指示書と合わせておいておくためのカンバンなのですが、モニターの土台の上に置きます。モニターの土台には金属が使われているので、直接カンバンを置いただけでは、RFIDが誤検知されてしまうので、高さが必要だったんです。この治具は300個必要でしたが、以前のFDMの3Dプリンターでは5個を30時間かけて作っていました。それがCarbon社のM2では25個を9時間半弱で造形できます。
―単純に考えて16分の1の時間に短縮できたんですね、、すごい効率化です。
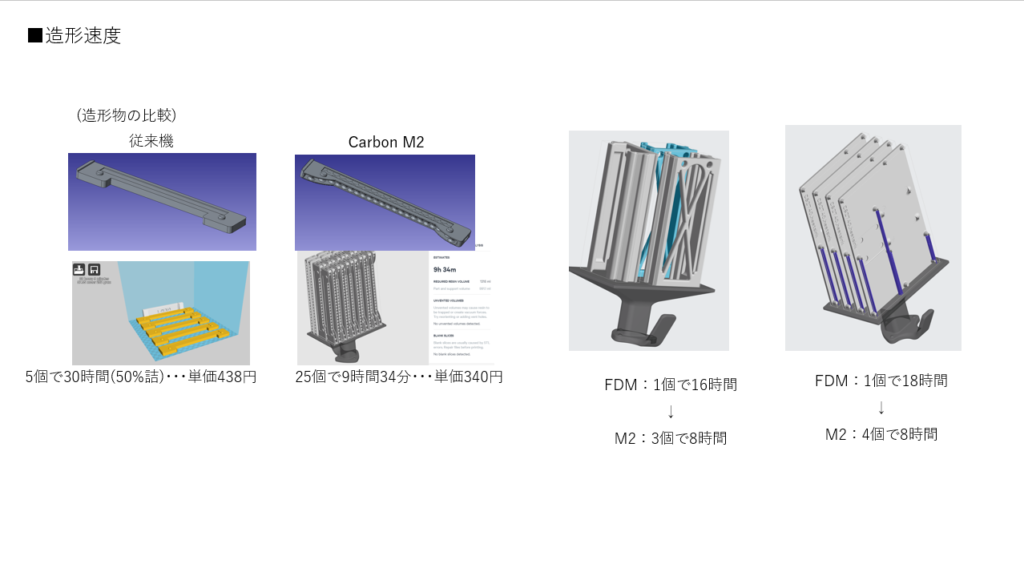
造形所要時間を16分の1に短縮
そうですね。いままで3Dプリンターの守備範囲は1個から数十個だとおもっていましたが、数百個の部品も用意できるということがわかって視野が広がりました。Carbon社の材料価格はFDM方式のフィラメントとそんなに大きく変わらないので、コストパフォーマンスは非常に良いと感じています。
ようやく現場の声に向き合える体制になった
―こうして実際に狙い通りの治具を自由に作れるようになって、周りからの反応はどうでしたか?リクエストなどでてきましたか?
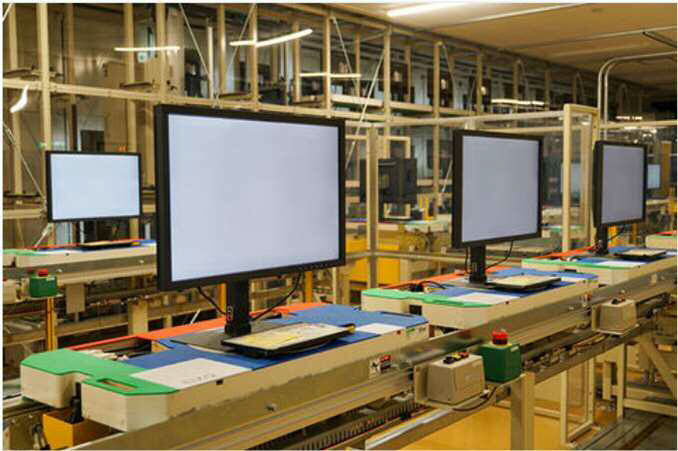
製造現場の風景
正直にお伝えすると、外注加工やFDM方式3Dプリンターでは、コストや時間がかかり過ぎて、現場の要望に応えられなかったことも多かったんです。ですがCarbon社の3Dプリンターを導入してから、コストも削減でき、時間にも素早く対応できるようになってきました。ようやく現場の声を拾って、タイムリーに改善していくことが物理的に可能になってきました。今まさに『現場の声に向き合えるようになってきた』というところです。
―少量多品種生産だと、生産期間も短いですもんね。今日拾った声を明日改善できるようになった。そんな大きな変化のように聞こえます。こうした現状での手ごたえを踏まえて、今後はどのような活用法をお考えですか?
製品の最終部品の製造にも活用していけたら面白いと思っています。3Dプリンターを活用しているのは生産技術部門が多いですが、製品設計部門でも活用していますので、メリットがあれば製品の最終部品への使用も考えています。
―従来の設計や製造の在り方で大きな問題がない場合は、取り組むのが難しいですよね。保守部品などから取り組まれるケースも増えてきていますが、EIZOさんの場合いかがですか?
いままでの考え方、やり方で最適化されているところを変えるのは、製品の最終部品ではいっそう大変だと思います。そういう意味でCarbon社のノウハウをもっと利用する機会があっても良いかなと思っています。
今回取材をお受けする前に、山本光学さんの事例記事を読んだのですが、その中でサブスクリプションの中で設計支援をかなり手厚く受けていることが紹介されていました。当社では利用する際にあまり困らなかったので、ほとんどCarbon社の設計支援を利用してきませんでしたが、こんな点が大きく改善できるなど具体的な変更点を、見える形にして支援頂いており、興味深い内容でした。
***
導入から担当したJSR銅木氏を交え、終始和やかな取材だったが、非常にオープンに製造現場も見学させていただき、気になるコスト削減効果に関しても具体的にご教示いただけた。これはEIZOが積極的に工場見学を受け入れる文化であることも大きいが、狙った導入効果がきちんと出ている手ごたえがあるがゆえだろう。次のページ以降では、専氏が語ってくれたEIZOの実例を取材する中で見えてきた「なぜ順調に3Dプリンター活用が現場に浸透できたか」に関してあらためて整理してみたい。そこには4つほどポイントがあるように思われる。
成果を飛躍的に拡大させた4つの要因
EIZOはCarbon社のM2プリンター導入以前からFDM方式の3Dプリンターをつかって成果を上げていた。それが2019年のライン新設のタイミングで新規にM2プリンターを導入することで適用範囲を拡大することができた。その理由はなんなのか。専氏の話から考えてみると、この理由には以下の4点が要因として考えられる。
- 少量多品種生産で治具を実際に製造していた(実需があった)
- 材料が多彩でアルミから材料置換できた(改善効果を説明しやすい代表事例があった)
- 材料コストが安い(普段使いできるレベルだった)
- 造形が安定しており早い(道具として信頼できた)
以下それぞれの要因についてみていきたい。
要因1:3Dプリンターで造形するモノへの実需があった
もっとも大きな観点としては、実際に治具をたくさん用意していた、という実績だ。実需として「用意する必要があるモノ」がある程度の量、存在していて、その分量も予算として可視化されていた。この点が非常に具体的に導入効果を算定する際にものをいったはずだ。調達コストを比較することで明らかにコストメリットがみえれば、導入の障壁は大きく下がるし、経営も理解できる。
一方で、EIZOでは治具の取り違えを防ぐために意匠にこだわって一目で違いがわかる治具を製作することはあっても、「3Dプリンターならではの設計」には取り組んでいない。3Dプリンターならではの設計に時間を割かなくても、治具を必要なタイミングで製作し、狙い通りのコストダウンを実現できているからだ。3Dプリンター活用は手段であって目的ではないことを理解して、主体的に活用していることが非常に伝わるエピソードのように思う。生産技術部門が推進しなければいけないタスクは山ほどある。道具として使う使い方は使い手に託されているのだ。治具製作の場合、3Dプリンターならではの先進的な設計に取り組む意義はあっても、必須条件ではないことをEIZOは身をもって証明してくれたように思う。
要因2:3Dプリンターの導入効果を体感できる象徴的な事例があった
実際に計画通り実施ができるかどうかは導入してみないと判断できない。しかし、たとえばアルミの削り出し固定治具のように1部品の調達コストが数万円で1セットの価格が二けた万円以上だったのが、3Dプリンターで造形すると数千円程度、など明確に見込める場合は、導入効果を評価しやすい。この部品でうまく活用できれば大丈夫、という合格ラインを設定しやすい点は導入推進者や利用者が投資に対する効果を過大に期待されずに済むために、あったほうが良い評価ポイントだ。こうしたわかりやすい事例を耳にした現場から相談が舞い込むようになり、活用範囲が広がってきたという。
要因3:3Dプリンターの利用費用が普段使いできるレベルだった
せっかく導入しても「材料費が高いから気軽に使いにくい」、「機材が使いにくく一部の人間しか使えない」などの場合は、多用途に展開することは難しかっただろう。しかしCarbon社のM2プリンターは材料費が非常に安価だ、許容範囲だと感じることができたために、いろいろな治具の製作にも利用してみようとチャレンジができる下地をつくることができた。
材料コストに関しては、Carbon社独自の取り組みとして、ユーザーの使用量が多い場合、一定以上の量をまとめて発注するとボリュームディスカウントが適用される。FDM方式の3Dプリンターの材料費が1グラム5円程度だったのが、Carbon社の3Dプリンターでもっともコストパフォーマンスがよい材料は1グラム8円程度で使用できる。1グラム3円程度の差しか発生しないので、FDM方式のフィラメントとほぼ同じ感覚で造形できているとのことだった。
材料費をおそれず挑戦できる安心感は、3Dプリンターを普段使いするほど利用を定着化させることに貢献した。3Dプリンターが特別な道具ではない、というレベルで利用できる雰囲気を醸成できたことが2年間で200種類以上の治具を製作できた背景に存在することは間違いない。
要因4:3Dプリンターを道具として信頼できた
いくらコストやリードタイムで優位性があっても、設計者が自分で使いこなせない、造形の安定性が低く失敗が多いなどの状況だと継続的な活用は難しい。度々造形に失敗して目標の納期を守れないことが続いていたら、EIZO社内でも一部の熟練者しか利用できない運用になっていただろうし、ゆとりがある納期のものを造形するためだけに利用されていただろう。
しかしEIZOでは、諸般の都合でほかの調達方法では間に合わないものは3Dプリンターで調達することが当たり前になっているという。これは、造形が安定しており、設計者の期待に応えている証拠だ。利用者が「この機械はこれくらいの速さで造形できるはず」と読んだ納期を実現できることは信頼につながる。この信頼にこたえている実績が社内利用の拡大につながっていることは間違いない。
3Dプリンターによる治具製作で結果をだすための4つのポイント
『3Dプリンターならではの設計』に取り組まなくても治具製造などの現場で大きなコスト改善、納期短縮を実現してきたEIZOの3Dプリンター活用事例は、日本の多くの製造現場の有力なロールモデルになりうる。先ほど触れた成功の4つの要因は、裏返せば導入して効果をだせるかどうかを判断する基準にもなる。
- ポイント1:作るモノの物量がある程度あるか
- ポイント2:導入効果を定量化でき納得感がえられそうな象徴的なケースが設定できるか
- ポイント3:3Dプリンターの導入費用・利用費用が予算範囲か
- ポイント4:3Dプリンターを道具として信頼できるか
ポイント1の「作るモノの物量がある程度あるか」に関して、ぜんぜん思い当たらない、経営層に説明できるだけの物量がない場合は、そもそも土台に乗りにくい。いまなくてもうまくいけば取り組めるという想定が思いつく段階までは事前に洗い出しをしておく必要があるだろう。なんとなく思いついている場合は、事前に3Dプリンターメーカーに相談してみるのも手だ。たとえばCarbon社に治具調達に関して相談すれば、実際に現場を見ながらさまざまな事例をもとにアイディアをくれるだろう。
ポイント2の「導入効果をえられそうな象徴的なケースが設定できるか」に関しては、たとえばアルミの削り出し固定治具を樹脂に材料置換し、造形できるかという導入効果がおおきそうな命題を設定することを意味する。いろいろつかえそうだが、導入効果や納期短縮効果が低い事例ばかりつたえても経営は納得しない。大きなわかりやすい効果を見せることは導入検討の重要なマイルストーンのように思われる。
ポイント3の「3Dプリンターの導入費用・利用費用が予算範囲か」に関しては、経営層こそ、いままで多種多様な生産設備の導入検討を行ってきたプロだ。投資の意思決定をするのが仕事だといっても過言ではない。とはいえ、そもそも購入が難しい高額の機種はいくら検討しても経営層のコミットを得ることが難しいケースも多いだろう。
ポイント4の「3Dプリンターを道具として信頼できるか」に関しては、実際に利用してみないことには判断できないが、サンプル造形を依頼して仕上がりを確認する、従来の方法と比較検討するなどの方法で、目線ずれが起こらないようにコントロールしていく必要がある。チャンピオンデータとよばれるような展示会に並んでいるプロ中のプロが時間をかけて完成度を上げた造形サンプルで評価を行うのではなく、実際に自分たちが作成したデータをもとにした造形をもとに評価を行っていく必要があるだろう。
すべてのポイントを事前にクリアすることができない場合でも、導入してみて何がよくなるか、経営課題や現場の課題を解決するために価値がある投資かを検討し、価値があると判断できれば導入できる可能性は大いにある。たとえば生産準備を担当するメンバーが人手不足で現場が疲弊している場合、Carbon社のサブスクリプション契約であれば、作りたい治具に関して設計支援を受けることができるかもしれない。各社状況が異なるので、先ほどあげた4つのポイントを基に、自社の課題を解決するために3Dプリンター活用を検討していくことが重要だ。
現実問題、現場の改善要望をすべて形にすることは難しい。ある部分、聞き流してきたというEIZO専氏の声は現実的な対応だったことだろう。しかし3Dプリンターの活用範囲を拡大することで、専氏はこの妥協を乗り越えて、改善を大きく進めた。想定できるコスト削減効果を3Dプリンターの減価償却までシミュレーションして予算取りを行い、そうした現実的な妥協を覆す取り組みには学ぶべき点が多いように思われる。3Dプリンターを活用した治具製作を具体的に検討している方は実際にこうした観点で取り組み方を検討してみてほしい。自分たちの会社にフィットした3Dプリンター活用を推進している企業は今も日本中で増えている。さあ、次はあなたの番だ。
ShareLab NEWS掲載ページはこちら