反復的な設計アプローチと、Carbon技術によりもたらされた認定までの大幅な時間短縮を通し、製造パートナーであるThe Technology House(TTH)はNASAと協力して、新しい自律飛行検査ロボットSeekerに使われる冷ガス推進システム用の4つの高性能スラスタを迅速かつ低コストで製造しました。Seekerは、自律ロボット検査のためのNASA 自由飛行技術実証プロジェクトで、ノースロップ・グラマンが契約した11回目となる国際宇宙ステーション(ISS)への商用補給サービスのミッションとして、シグナス宇宙船で打ち上げられました(図1)。プロジェクトの開始から打ち上げまでが約1年という制約の下、NASAは一連の急速な統合システム設計サイクルの一環として、高度に最適化された推進コンポーネントを迅速に製造できる技術を必要としていました。以下では、 Carbonのアディティブ技術によってNASAチームがどの様に宇宙ハードウェアのアジャイル開発を成功させたのか、そしてCarbon Digital Light Synthesis™(DLS™)とプラスチック材料CE 221が新しいロボット工学への素早い取り組みのための実行可能な生産ソリューションとしてどの様に検証されたかについて説明します。
Seeker:自律飛行検査技術におけるNASAの最新投資
外部の自律飛行ロボット検査装置であるSeekerは新しいタイプのロボットです。Seekerはおよそ食パン一斤分の大きさで、NASAチームは一連のテストフライトにおいて、段階的に機能を強化した宇宙船を迅速に構築し実証するための反復設計サイクルのアプローチを選択しました。今回の打ち上げは、Seekerの最初のデモフライトです。軌道上で操縦するために、Seekerが搭載している冷ガス推進システムには、12個のスラスタに加え、回旋型ニューラルネットワークを使用する視覚ナビゲーションシステムをベースにしたガイダンスナビゲーション&コントロール(GN&C)システムが含まれています。このシステムは、視覚ナビゲーションのための広視野カメラに基づいて動作する一方で、詳細な検査のための狭視野カメラも搭載しています(図2)。
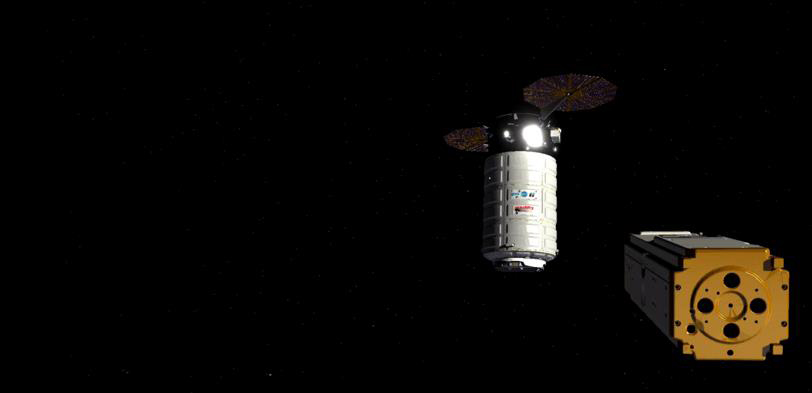
図 2:シグナス(左)の検査任務にむかう Seeker の自律移動のシミュレーション(右下)
宇宙ハードウェアのための迅速な開発への転換
Seekerの側面には、慣性測定装置(IMU)、レーザー距離計(LRF)、4つの太陽センサー、2台のカメラ、および通信アンテナといった、GN&Cシステムが動作するために必要な機器が大量に装備されています。およそ10 cm x 10 cmの同じ面上には、検査ロボットを動かすために4つの小型ロケットスラスタを統合する必要がありました。Seekerチームが抱えた問題は、4つの独立した冷却ガスジェット、ガスチューブの配管と固定具、それら部品をまとめて固定する部品といった重要なコンポーネントを、高度に制約されたスペース内に配置し、更には近接している他の全てのセンサーの設計を調整することにより、効率的な冷ガススラスターシステムを開発することでした(図3)。
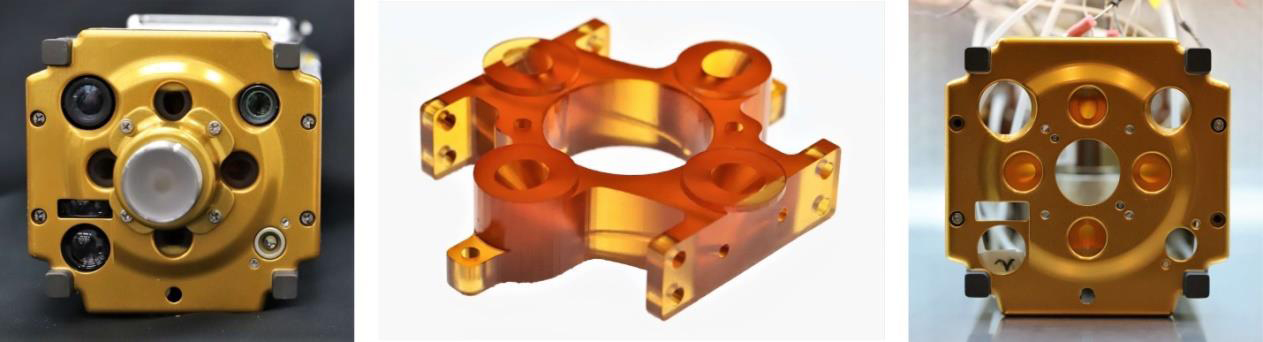
図 3:機器パッケージの最終レイアウト(左)および機器と金属面(右)との間に設置される CE 221 スラスタ(中央)。
チームは、システム設計が固まっていくにしたがい、これらの課題を解決するために、構築、テスト、および反復設計改良できる軽量の材料が必要であることを理解していきました。伝統的な機械加工または金型製造方法では、この非常に正確な冷ガス推進システムに必要とされる複雑なホールや通路を製造できません。迅速な設計改良が可能なCarbon Digital Light Synthesis™(DLS™)と最終製品レベルの部品品質によって、この高性能部品用途に理想的な生産ソリューションであることが検証されました。NASAは10回以上の設計修正を繰り返し、ポストマシニングを必要とせずに、複雑な統合コンポーネントを製造することができ、認証までの時間を大幅に短縮させることができました。
高性能CE 221材料

図 4: 1200 psi 以上の圧力で破裂することが確認されたスラスタ
地上オペレータの周りで使用される加圧部品、しかもそれが軌道中に使用される場合、その部品のための新しい技術や材料の適用は、NASAにとって長い認証プロセスの対象となります。特に新規の材料や製造方法に関しては、参入障壁が高い厳しい設計基準や建築基準で評価されます。
Seeker以前に、地上および飛行中のオペレータ周りで使用される3Dプリントされた加圧プラスチック部品がNASAによって認証された例はありませんでした。シアン酸エステル(CE 221)が提案されたとき、NASAの中では、非金属材料がNASAの要求を満たせないのではないかとの疑念がありました。これらの問題に対処するため、Seekerチームは、コンポーネントの機能を理解するための広範な開発および認定テストのスケジュールを設定するとともに、プロセス変動をスクリーニングするためのテスト方法を設定しました。この開発プログラムの一環として、チームは100回以上の失敗を圧力試験で重ね、構造設計とシーリングインターフェースを改善させました(図4)。
正確で再現可能な生産プロセス
TTHがこのマニホールドを製造したとき、彼らは部品に複数の変動が生じていることに気づきました。そこでTTHはNASAと協力し、部品の機能を維持しながら精度とプリント性を向上させるためのデザイン要素を追加しました。予測可能な機械的特性と部品性能の必要性を考慮し、TTHは後処理と硬化時間を見直しました。最終的に確立された再現性のあるプロセスにより、プロセス変動を効果的に制御することができ、極端に小さな炉口部の寸法(0.026インチ)の限界公差を満たすに至りました。
最終的にこのアプローチはうまくいき、CarbonのCE 221材料がプロジェクトで要求された安全性と性能の要求を全て満たし、その部品が飛行使用に認定されました。
「アディティブマニュファクチャリングに使用される他のプラスチックでは、このプロセス全体を通過することはできません。それは加圧に耐え、宇宙の寒さに耐え、太陽の熱に耐えなければなりません…CarbonのCE 221がこれを成し遂げました。そしてこれこそが、NASAがアディティブ技術で作り出すことができた全ての理由でした。」
Greg Cebular
The Technology House 営業担当副社長
検証済、迅速性、コスト効率性:打ち上げ準備完了
TTHとの製造プロセス全体に真の設計柔軟性を持たせることで、NASAは改良期間を短縮し、宇宙ハードウェアのアジャイル開発の成功を実証することができました。これは、素早く組み立て、テスト、そして反復改良する能力を大いに向上させ、アイデアからプロジェクトの開始、そして打ち上げまでに1年あまりの短時間で可能にしました。これはNASA史上でも前例がありません!NASAはこのプログラム全体を300万ドル以下で実行したため、非常に効率的なプログラムとなりました。
Carbon DLS技術を通じてTTHがNASAをサポートできたのは、オンデマンド生産の能力によるものです。それは、NASAの厳しい機械的要件を満たす再現性のある製造プロセスとして証明されただけでなく、その材料が、高性能かつ宇宙仕様として使えることも証明されました。TTHの仕事が示したのは、Carbon DLS™技術のようなもので部品を作ることによって、新しい技術とプラスチック材料で、迅速かつ費用対効果の高い方法でSeekerのような検査ロボットを開発できるということです。