製品開発の現場では、プラスチック部品の製造を射出成形に依存する状態が何十年も続いてきました。射出成形は長年の実績もあり、頑強性、反復性に優れ、量産に適しています。射出成型を使った場合の製造コストを考える際、直接材料、作業時間、直接人件費¹ の面だけでコストを検討するのが一般的です(図1)。しかし、この従来のコストモデルは、感覚的にわかりやすいものの、射出成形による部品製造に伴う真の総コストが反映されていないのです。
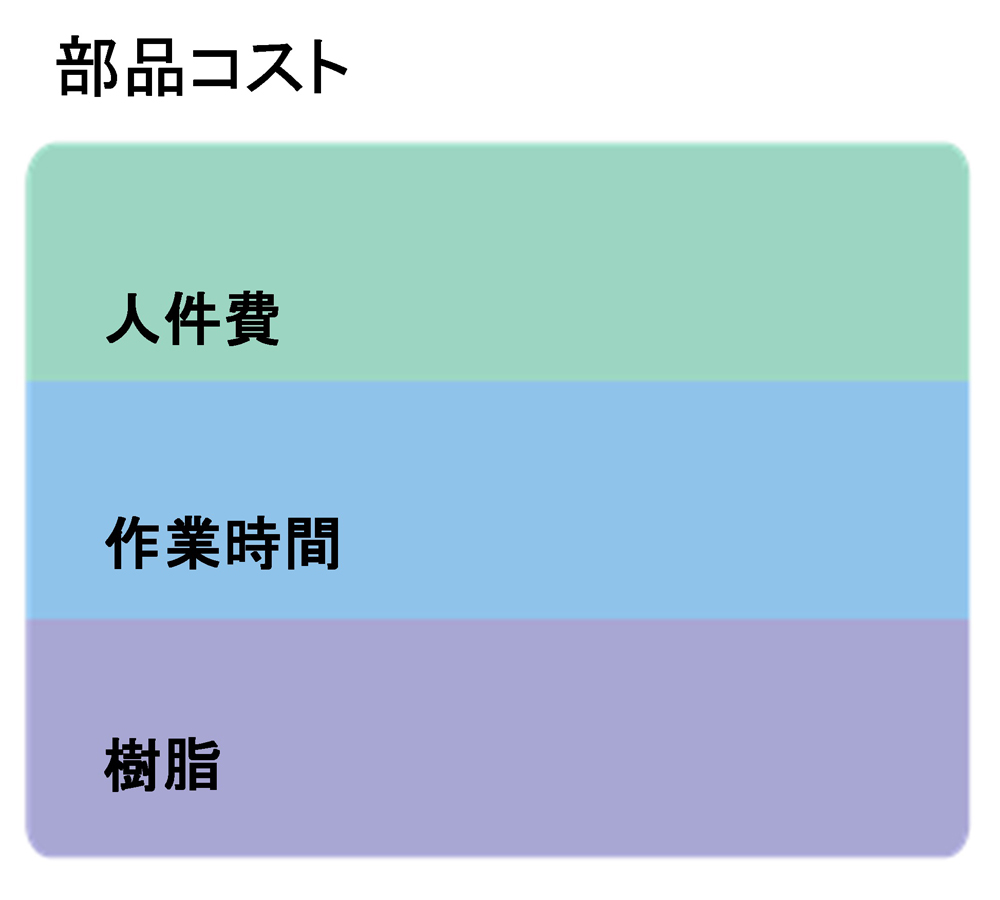
図1:射出成形の従来のコストモデル
現実には、機械エンジニアや工作機械の技術者、製品開発チームは、射出成形の実際の製造コストが従来のコストモデルの試算を大幅に上回る事実に気づくことになります。もっと具体的に言えば、従来のコストモデルでは(1)工作機械の償却、(2)試作・段取り替え、(3)射出成形プロセスの設計、(4)段取り費用、(5)最小発注数量(MOQ)による過剰在庫という、射出成形に伴う5つの原価要素が抜け落ちています(図2)。
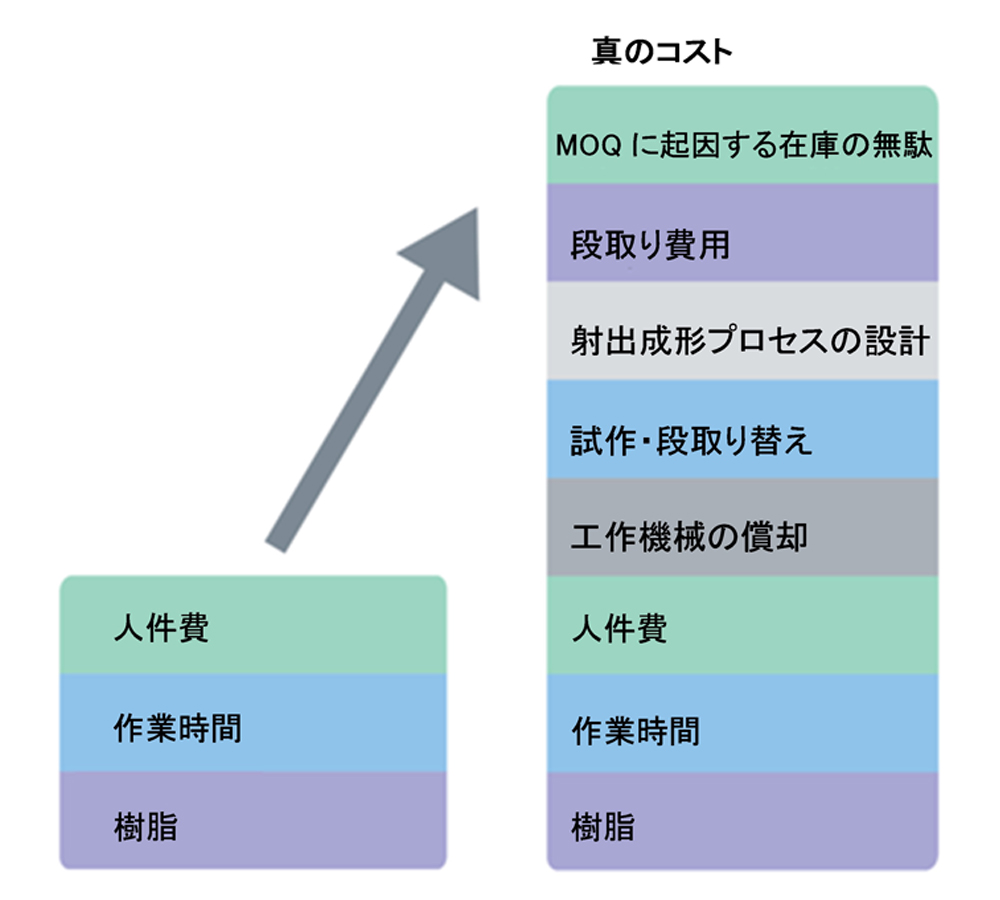
図2:射出成形の従来のコストモデルと新しいコストモデルの比較
射出成形プロセスは、すでに数十年にわたる製造実績もあって、特徴がはっきりしています。ところが、射出成形による部品製造の真のコストはまだ十分に理解されていません。典型的なのは試作段階での工作機械の償却と段取り替えで、こうしたコストは、当初製造見積もりには含まれません。工作機械の入れ替えのたびに5千ドルから5万ドル(適用分野による)が上乗せされるなど、金型・治工具関連コストは簡単に積み上がり、総コストを押し上げていきます。
また、射出成形プロセスの設計に伴う時間と人件費も、通常は総コストに含まれない重要コストです。金型設計についても、製造のゴーサインが出るまでにパーティングラインの位置、シャットオフ、抜き勾配、フィレット、ゲート、エジェクタピンなど重要な設計要素を正確に適用する必要があります。しかも、込み入った形状やテクスチャ、均一ではない肉厚といった複雑な条件の部品の場合、膨大なコストと時間が必要になる恐れがあります。段取り費用には、射出成形機への金型セット、試し成形、成形作業の調整など一連の作業に要する時間や人件費が反映されます。短期の射出成形作業では、ほとんどの場合、これがかなりの追加負担になります。
最後に、射出成形に伴う金型作成コストが膨らめば、当然、先行投資した工作機械コストを償却するため、大量生産用のプロセスを選ぶ傾向が生まれます。しかし、このように数量を増やして償却しようとしても、多くの製品開発チームにとっては効果がありません。受託製造会社は、不当に高い金型・治工具コストを最小発注数量(MOQ)要件に隠していることが多いからです。つまり、この要件から言えるのは、製品開発チームが必要とする部品は数百個だとしても、数千個単位で部品を発注しなければならないのです。また、MOQがあると、在庫保有コストやそれに伴う部品の無駄につながる可能性があり、組織の他の事業やサプライチェーン担当チームにもしわ寄せが行きかねません。国立標準技術研究所(NIST)² の報告によれば、2011年に製造業界で在庫のまま死蔵されている部品は5370億ドル相当に上ります。この数字は時間の経過とともに増加していったと思われます。しかし、アディティブ・マニュファクチャリングとオンデマンド生産の仕組みがあれば、在庫保有コストとそれに伴う無駄を削減する完璧なソリューションに今や手が届くようになりました。
市場投入までのコスト
Carbonのパートナーの多くにとっては、射出成形プロセスの最初から最後まで遅れが頻発するために、製品を期日までに発売することが大きな課題となっています。どの業界であれ、期日を守ることは重要ですが、消費者向け製品や産業用エレクトロニクスなど特に競争の激しい業界ではなおさらのことです。こうした市場では市場投入の期待に応えられずに遅れが発生すれば、有力な競合他社に売り上げや市場シェアを奪われることにもなりかねません。産業用エレクトロニクスの場合、遅れは往々にして部品がデザインされても、最終製品に至らず、数年に及ぶ売り上げの損失につながる恐れがあります。
図3に示すように、射出成形品の開発スケジュールは長期にわたり、6週間から23週間と大きな幅があります。射出成形と金型の調整が加わるだけで、全体のスケジュールに2〜7週間が上乗せされます。また、金型製作は特に所要期間の変動が激しく、製作方法(外注か内製化か)にもよりますが、完成までに2〜12週間かかるのが一般的です。製造プロセスの選定の際、正確に見積もるには、射出成形に伴う時間と変動幅を考慮しなければなりません。
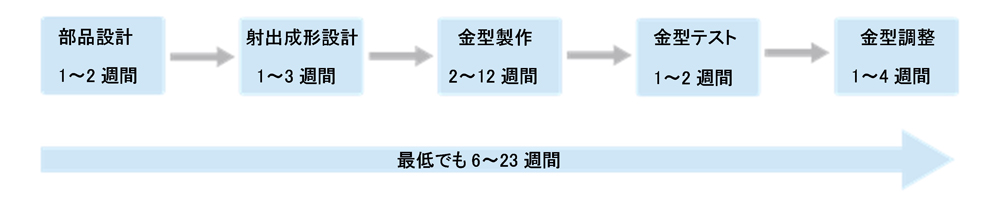
図3:射出成形品開発のタイムテーブル
まとめ
Carbonでは、アディティブ・マニュファクチャリングの世界に馴染みのないお客様でも、その特有のメリットを享受していただける技術を提供しています。主なメリットとしては、(a) 射出成形に比べて先行投資費用が少ない、(b)アジャイル型の部品製造、(c)デザイン変更時も素早い修正が可能、(d)臨時のエンジニアリング費用が少ない、といった点が挙げられます。さらに、射出成形が最終部品の製造方法として最も効率的とは言えないことを示すビジネス・シナリオもあります。こうしたシナリオにおいて、CarbonのDigital Light Synthesis™技術は、従来技術にない明らかな優位性があります。具体的なシナリオとして次の例が挙げられます。
- 成形不可能とされる形状(込み入った溝や穴、凹部がある複雑な部品など)
- Carbonならではの優れた機能(精密設計可能なラティス、テクスチャ、発泡材料代替)
- 部品の統合(複数部品を組み合わせることなく、単一部品として3D造形可能、シンプルな製造ライン)
- サプライチェーンのスリム化(部品のオンデマンド生産、サプライヤーへの依存度低減)
すでに数々の産業用・民生用の製品メーカーが、少量生産部品を中心に、射出成形部品の調達や保守から脱却し、Carbonの技術を使った部品のオンデマンド生産に乗り出しています。射出成形品の典型的な開発期間である6〜23週間と比較して、Carbonの技術では、変動幅を大きく抑え込み、2〜3週間にまで製造プロセスを短縮できます。
さらに、エンジニアや製品開発チームにとって、Carbonの技術は設計面で新たな自由をもたらし、製品設計のあり方を見直すきっかけにもなります。全体的に見れば、Carbonの技術は射出成形を補完する関係にあり、最終的な用途やユースケースに最適な方法の選択はお客様に委ねられています。その際、ここでご紹介した視点から射出成形の真のコストを算定し、そのうえで判断を下すことが大切です。
製品開発の現場でサプライチェーンのスリム化とアジャイル化を推進し、画期的な製品を市場投入するにはどうすればいいのか。その鍵を握るのがCarbonの技術です。
¹製造間接費は必ず発生しますが、簡略化のためここでは省略してあります。
²Costs and Cost Effectiveness of Additive Manufacturing, NIST Special Publications 1176, Dec. 2014